Category
All
New Technology
Service & Software
Internet & Communication
Electronics & Semiconductor
Pharma & Healthcare
Other
Energy & Power
Agriculture
Consumer Goods
Machinery & Equipment
Food & Beverages
Medical Care
Automobile & Transportation
Packaging
Chemical & Material
Medical Devices & Consumables
Category
All
Total: 13 records, 2 pages
Search For: Chamber Components
Global Chamber Components Market 2024 by Manufacturers, Regions, Type and Application, Forecast to 2030
03 Jan 2024
Electronics & Semiconductor
According to our (Global Info Research) latest study, the global Chamber Components market size was valued at USD million in 2023 and is forecast to a readjusted size of USD million by 2030 with a CAGR of % during review period.
USD3480.00
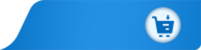
Add To Cart
Global PVD and ALD Coating for Chamber Components Supply, Demand and Key Producers, 2024-2030
27 Jun 2024
Electronics & Semiconductor
PVD and ALD Coating for Chamber Components
PVD and ALD coatings for chamber components are typically based on yttrium or aluminum oxides or may be made from aluminum oxynitride (AlON). The exact chemistry and coating thickness must be tailored to the application. The use of temperature in the chamber, processing time, and gases vary considerably depending on the device specifications, and these variables are used to select the right combination of coatings for their desired coating performance. Custom precision-engineered coatings provide the optimal balance between cost and performance. Deposition chambers contain various parts and components that either contact the device wafer directly or are exposed to process chemicals that subsequently reach the wafer. As such, material selection is critical. The corrosive chemicals used in plasma-etch chambers attack the tool component surfaces and degrade coatings. Longer exposure to hotter plasmas, which is common for 3D device processing, accelerates degradation. Particles shed from the corroded surfaces then deposit on the wafers, potentially causing device failure. Components protected with yttrium oxide deposited by plasma spray-coating or made from anodized aluminum have long been the industry norm. Although such solutions have worked for many years, the nano-scale features of advanced process nodes demand an increased level of cleanliness for every part in the system. Conventionally coated components are not rugged enough to withstand the aggressive environments inside etch and deposition chambers without impacting device yield. Plasma spray coatings are relatively rough and porous, while anodized coatings exhibit in-situ cracking that makes them degrade too readily. The complex shapes of parts inside deposition chambers also pose a challenge for spray coating, which works best when coating planar surfaces. Precision engineered, specialized coatings borrow vacuum thin film technologies associated with semiconductor wafer processing to produce coated components that can better resist the corrosion and oxidation that degrade conventional coatings. Two options are available: physical vapor deposition (PVD) and atomic layer deposition (ALD). Every precision engineered coating must exhibit a minimum level of wear and corrosion resistance in the presence of corrosive plasma/chemistry and adhere fully to the underlying substrate to create a uniformly coated surface. The geometry and material of the part being coated, the type of chamber, and the processing conditions further dictate the optimal coating chemistry and method.
USD4480.00
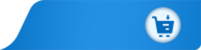
Add To Cart
Global PVD and ALD Coating for Chamber Components Market 2024 by Company, Regions, Type and Application, Forecast to 2030
27 Jun 2024
Electronics & Semiconductor
PVD and ALD Coating for Chamber Components
PVD and ALD coatings for chamber components are typically based on yttrium or aluminum oxides or may be made from aluminum oxynitride (AlON). The exact chemistry and coating thickness must be tailored to the application. The use of temperature in the chamber, processing time, and gases vary considerably depending on the device specifications, and these variables are used to select the right combination of coatings for their desired coating performance. Custom precision-engineered coatings provide the optimal balance between cost and performance. Deposition chambers contain various parts and components that either contact the device wafer directly or are exposed to process chemicals that subsequently reach the wafer. As such, material selection is critical. The corrosive chemicals used in plasma-etch chambers attack the tool component surfaces and degrade coatings. Longer exposure to hotter plasmas, which is common for 3D device processing, accelerates degradation. Particles shed from the corroded surfaces then deposit on the wafers, potentially causing device failure. Components protected with yttrium oxide deposited by plasma spray-coating or made from anodized aluminum have long been the industry norm. Although such solutions have worked for many years, the nano-scale features of advanced process nodes demand an increased level of cleanliness for every part in the system. Conventionally coated components are not rugged enough to withstand the aggressive environments inside etch and deposition chambers without impacting device yield. Plasma spray coatings are relatively rough and porous, while anodized coatings exhibit in-situ cracking that makes them degrade too readily. The complex shapes of parts inside deposition chambers also pose a challenge for spray coating, which works best when coating planar surfaces. Precision engineered, specialized coatings borrow vacuum thin film technologies associated with semiconductor wafer processing to produce coated components that can better resist the corrosion and oxidation that degrade conventional coatings. Two options are available: physical vapor deposition (PVD) and atomic layer deposition (ALD). Every precision engineered coating must exhibit a minimum level of wear and corrosion resistance in the presence of corrosive plasma/chemistry and adhere fully to the underlying substrate to create a uniformly coated surface. The geometry and material of the part being coated, the type of chamber, and the processing conditions further dictate the optimal coating chemistry and method.
USD3480.00
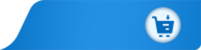
Add To Cart
Global CVD, PVD and ALD Coating for Chamber Components Supply, Demand and Key Producers, 2024-2030
20 Jun 2024
Electronics & Semiconductor
CVD, PVD and ALD Coating for Chamber Components
PVD and ALD coatings for chamber components are typically based on yttrium or aluminum oxides or may be made from aluminum oxynitride (AlON). The exact chemistry and coating thickness must be tailored to the application. The use of temperature in the chamber, processing time, and gases vary considerably depending on the device specifications, and these variables are used to select the right combination of coatings for their desired coating performance. Custom precision-engineered coatings provide the optimal balance between cost and performance.
USD4480.00
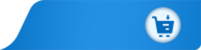
Add To Cart
Global CVD, PVD and ALD Coating for Chamber Components Market 2024 by Company, Regions, Type and Application, Forecast to 2030
20 Jun 2024
Electronics & Semiconductor
CVD, PVD and ALD Coating for Chamber Components
PVD and ALD coatings for chamber components are typically based on yttrium or aluminum oxides or may be made from aluminum oxynitride (AlON). The exact chemistry and coating thickness must be tailored to the application. The use of temperature in the chamber, processing time, and gases vary considerably depending on the device specifications, and these variables are used to select the right combination of coatings for their desired coating performance. Custom precision-engineered coatings provide the optimal balance between cost and performance.
USD3480.00
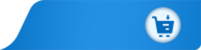
Add To Cart
Global Ceramic Chamber Components for Semiconductor Equipment Supply, Demand and Key Producers, 2024-2030
04 Mar 2024
Electronics & Semiconductor
Ceramic Chamber Components for Semiconductor Equipment
The global Ceramic Chamber Components for Semiconductor Equipment market size is expected to reach $ 958.6 million by 2030, rising at a market growth of 5.4% CAGR during the forecast period (2024-2030).
USD4480.00
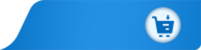
Add To Cart
Global Ceramic Chamber Components for Semiconductor Equipment Market 2024 by Company, Regions, Type and Application, Forecast to 2030
16 Jan 2024
Electronics & Semiconductor
Ceramic Chamber Components for Semiconductor Equipment
According to our (Global Info Research) latest study, the global Ceramic Chamber Components for Semiconductor Equipment market size was valued at USD 662.6 million in 2023 and is forecast to a readjusted size of USD 958.6 million by 2030 with a CAGR of 5.4% during review period.
USD3480.00
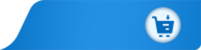
Add To Cart
Global Chamber Components Supply, Demand and Key Producers, 2023-2029
23 Jan 2023
Electronics & Semiconductor
The global Chamber Components market size is expected to reach $ million by 2029, rising at a market growth of % CAGR during the forecast period (2023-2029).
USD4480.00
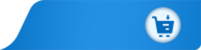
Add To Cart
Global Chamber Components Market 2023 by Manufacturers, Regions, Type and Application, Forecast to 2029
10 Jan 2023
Electronics & Semiconductor
According to our (Global Info Research) latest study, the global Chamber Components market size was valued at USD million in 2022 and is forecast to a readjusted size of USD million by 2029 with a CAGR of % during review period. The influence of COVID-19 and the Russia-Ukraine War were considered while estimating market sizes.
USD3480.00
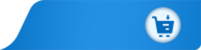
Add To Cart
Global PVD and ALD Coating for Chamber Components Supply, Demand and Key Producers, 2023-2029
19 Aug 2023
Electronics & Semiconductor
PVD and ALD Coating for Chamber Components
The global PVD and ALD Coating for Chamber Components market size is expected to reach $ million by 2029, rising at a market growth of % CAGR during the forecast period (2023-2029).
USD4480.00
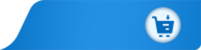
Add To Cart
- 1
- 2
Go To Page
Popular Product Keywords
Our Clients
What We Can Provide?
With better results and higher quality products,Our professional reports can achieve four things:
Insight into the industry market information
Analyze market development needs
Prospects for future development
Develop industry investment strategy
Search For: Chamber Components
Total: 13 records, 2 pages
According to our (Global Info Research) latest study, the global Chamber Components market size was valued at USD million in 2023 and is forecast to a readjusted size of USD million by 2030 with a CAGR of % during review period.
USD3480.00
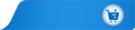
Add To Cart
PVD and ALD coatings for chamber components are typically based on yttrium or aluminum oxides or may be made from aluminum oxynitride (AlON). The exact chemistry and coating thickness must be tailored to the application. The use of temperature in the chamber, processing time, and gases vary considerably depending on the device specifications, and these variables are used to select the right combination of coatings for their desired coating performance. Custom precision-engineered coatings provide the optimal balance between cost and performance. Deposition chambers contain various parts and components that either contact the device wafer directly or are exposed to process chemicals that subsequently reach the wafer. As such, material selection is critical. The corrosive chemicals used in plasma-etch chambers attack the tool component surfaces and degrade coatings. Longer exposure to hotter plasmas, which is common for 3D device processing, accelerates degradation. Particles shed from the corroded surfaces then deposit on the wafers, potentially causing device failure. Components protected with yttrium oxide deposited by plasma spray-coating or made from anodized aluminum have long been the industry norm. Although such solutions have worked for many years, the nano-scale features of advanced process nodes demand an increased level of cleanliness for every part in the system. Conventionally coated components are not rugged enough to withstand the aggressive environments inside etch and deposition chambers without impacting device yield. Plasma spray coatings are relatively rough and porous, while anodized coatings exhibit in-situ cracking that makes them degrade too readily. The complex shapes of parts inside deposition chambers also pose a challenge for spray coating, which works best when coating planar surfaces. Precision engineered, specialized coatings borrow vacuum thin film technologies associated with semiconductor wafer processing to produce coated components that can better resist the corrosion and oxidation that degrade conventional coatings. Two options are available: physical vapor deposition (PVD) and atomic layer deposition (ALD). Every precision engineered coating must exhibit a minimum level of wear and corrosion resistance in the presence of corrosive plasma/chemistry and adhere fully to the underlying substrate to create a uniformly coated surface. The geometry and material of the part being coated, the type of chamber, and the processing conditions further dictate the optimal coating chemistry and method.
USD4480.00
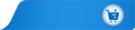
Add To Cart
PVD and ALD coatings for chamber components are typically based on yttrium or aluminum oxides or may be made from aluminum oxynitride (AlON). The exact chemistry and coating thickness must be tailored to the application. The use of temperature in the chamber, processing time, and gases vary considerably depending on the device specifications, and these variables are used to select the right combination of coatings for their desired coating performance. Custom precision-engineered coatings provide the optimal balance between cost and performance. Deposition chambers contain various parts and components that either contact the device wafer directly or are exposed to process chemicals that subsequently reach the wafer. As such, material selection is critical. The corrosive chemicals used in plasma-etch chambers attack the tool component surfaces and degrade coatings. Longer exposure to hotter plasmas, which is common for 3D device processing, accelerates degradation. Particles shed from the corroded surfaces then deposit on the wafers, potentially causing device failure. Components protected with yttrium oxide deposited by plasma spray-coating or made from anodized aluminum have long been the industry norm. Although such solutions have worked for many years, the nano-scale features of advanced process nodes demand an increased level of cleanliness for every part in the system. Conventionally coated components are not rugged enough to withstand the aggressive environments inside etch and deposition chambers without impacting device yield. Plasma spray coatings are relatively rough and porous, while anodized coatings exhibit in-situ cracking that makes them degrade too readily. The complex shapes of parts inside deposition chambers also pose a challenge for spray coating, which works best when coating planar surfaces. Precision engineered, specialized coatings borrow vacuum thin film technologies associated with semiconductor wafer processing to produce coated components that can better resist the corrosion and oxidation that degrade conventional coatings. Two options are available: physical vapor deposition (PVD) and atomic layer deposition (ALD). Every precision engineered coating must exhibit a minimum level of wear and corrosion resistance in the presence of corrosive plasma/chemistry and adhere fully to the underlying substrate to create a uniformly coated surface. The geometry and material of the part being coated, the type of chamber, and the processing conditions further dictate the optimal coating chemistry and method.
USD3480.00
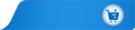
Add To Cart
PVD and ALD coatings for chamber components are typically based on yttrium or aluminum oxides or may be made from aluminum oxynitride (AlON). The exact chemistry and coating thickness must be tailored to the application. The use of temperature in the chamber, processing time, and gases vary considerably depending on the device specifications, and these variables are used to select the right combination of coatings for their desired coating performance. Custom precision-engineered coatings provide the optimal balance between cost and performance.
USD4480.00
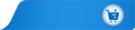
Add To Cart
PVD and ALD coatings for chamber components are typically based on yttrium or aluminum oxides or may be made from aluminum oxynitride (AlON). The exact chemistry and coating thickness must be tailored to the application. The use of temperature in the chamber, processing time, and gases vary considerably depending on the device specifications, and these variables are used to select the right combination of coatings for their desired coating performance. Custom precision-engineered coatings provide the optimal balance between cost and performance.
USD3480.00
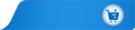
Add To Cart
The global Ceramic Chamber Components for Semiconductor Equipment market size is expected to reach $ 958.6 million by 2030, rising at a market growth of 5.4% CAGR during the forecast period (2024-2030).
USD4480.00
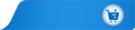
Add To Cart
According to our (Global Info Research) latest study, the global Ceramic Chamber Components for Semiconductor Equipment market size was valued at USD 662.6 million in 2023 and is forecast to a readjusted size of USD 958.6 million by 2030 with a CAGR of 5.4% during review period.
USD3480.00
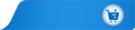
Add To Cart
The global Chamber Components market size is expected to reach $ million by 2029, rising at a market growth of % CAGR during the forecast period (2023-2029).
USD4480.00
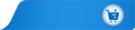
Add To Cart
According to our (Global Info Research) latest study, the global Chamber Components market size was valued at USD million in 2022 and is forecast to a readjusted size of USD million by 2029 with a CAGR of % during review period. The influence of COVID-19 and the Russia-Ukraine War were considered while estimating market sizes.
USD3480.00
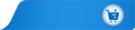
Add To Cart
The global PVD and ALD Coating for Chamber Components market size is expected to reach $ million by 2029, rising at a market growth of % CAGR during the forecast period (2023-2029).
USD4480.00
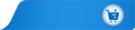
Add To Cart
- 1
- 2
Go To Page
Popular Product Keywords
- We Provide Professional, Accurate Market Analysis to Help You Stay Ahead of Your Competition.Speak to our analyst >>
Our Clients
What We Can Provide?
With better results and higher quality products,Our professional reports can achieve four things:
Insight into the industry market information
Analyze market development needs
Prospects for future development
Develop industry investment strategy
- Digging deeper into global industry information and providing market strategies.Contact Us >>